First I roughed out the shape on a band saw. Then it was time to start routing.
I decided to use the router table with the template router bit with the bottom mounted bearing to do the top. First I taped the template to the top. When I cut the mahogany I cut a depth of about 1/4" at a time. Since I was only using the table router with the mapleI decided just to cut the entire 5/8" top all in one swoop since the bearing of the bit had to reach all the way up across the maple to the template.
The key with this was to just take off a little bit of material at a time. I did this by not forcing the bearing through the excess wood all the way to the template. I just used the router bit to slowy shave off the wood until the bearing finally hit the template. This worked out pretty well although in some spots the wood burned a bit.
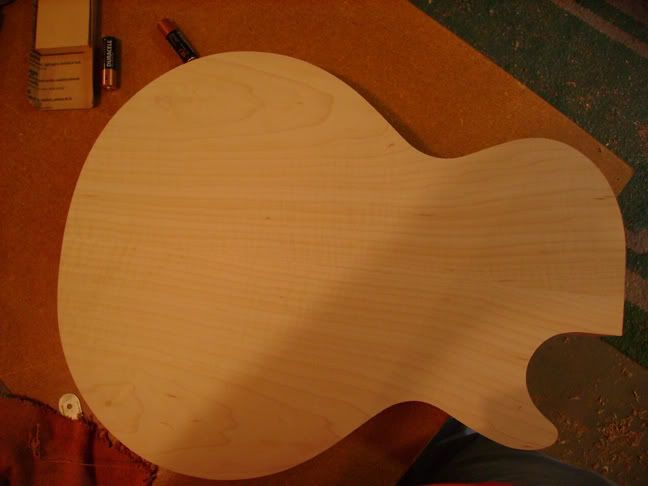
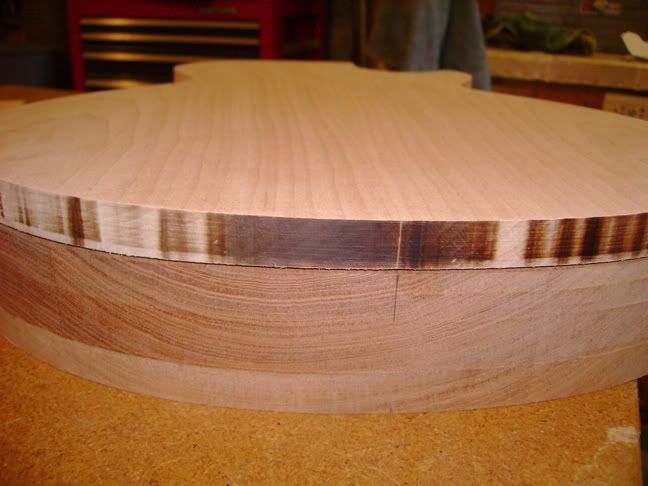
One important thing I left out. Usually you route counter-clockwise. However when you get close to areas where end grain could be a problem you want to route clockwise because it helps prevent the end grain from ripping out.
Here are some pics of the finished top resting on the mahogany body. I posted multiple pics so you could get a better idea of the flame pattern of the wood.
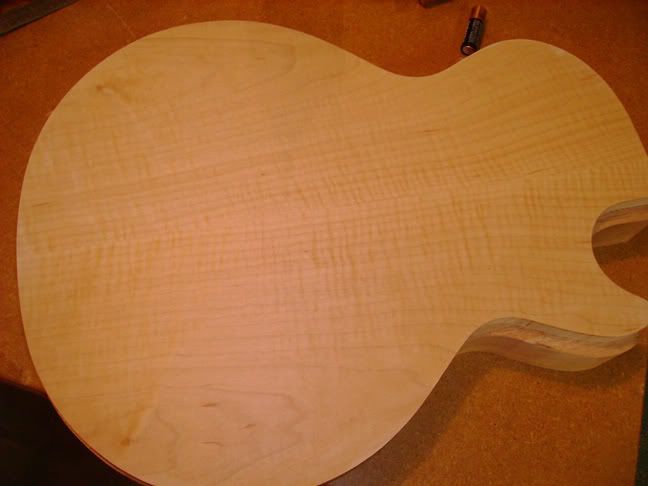
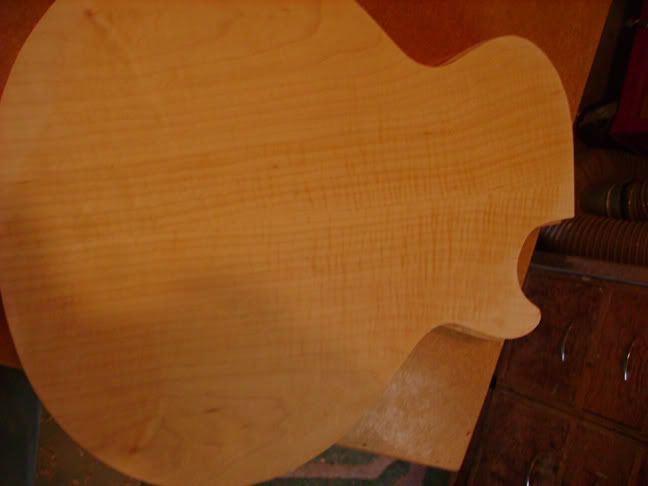

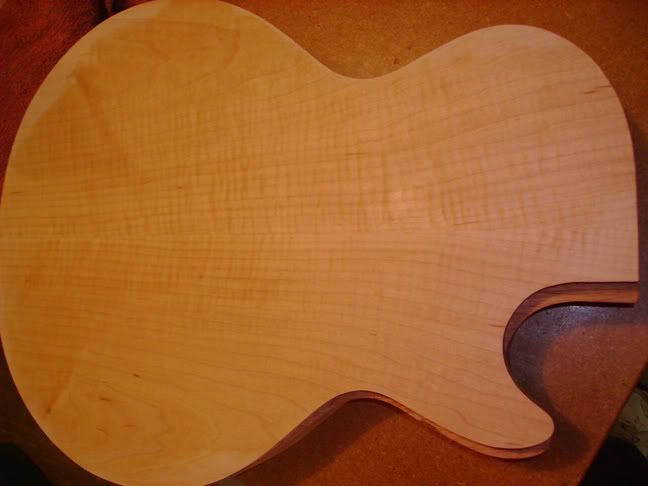
Next up gluing the maple top to the mahogany body.
2 comments:
looking really good rose. how on earth do you carve the top?
scott
There are three ways to do it that I know of. Once is a CNC machine. That is not an option for me or most hobby builders.
Another is to use a duplicarver which uses a probe to trace a top that's already been carved while a cutter cuts the exact carve in another piece of wood. Here's an example of a duplicarver:
http://www.tollway.com/archtop/started/duplicator.htm
The third method is to hand route steps in the body that lay out the carves and then use a finger plane to even things out.
I have a friend with a duplicarver so I'm probably going that route. I will be using a '59 Les Paul reissue to copy.
Post a Comment