The first thing that needed to happen was to get the board planed to close to 3/16" which is the size of the trus rod slot. You don't want to make it too small or it will have a loose fit. You don't want it too tight as all of the glue may squeeze out. So I ran the board through the DeWalt planer until it was close and then test fit it in the slot. I kept planing the board down a little at a time until it fit perfectly in the slot.
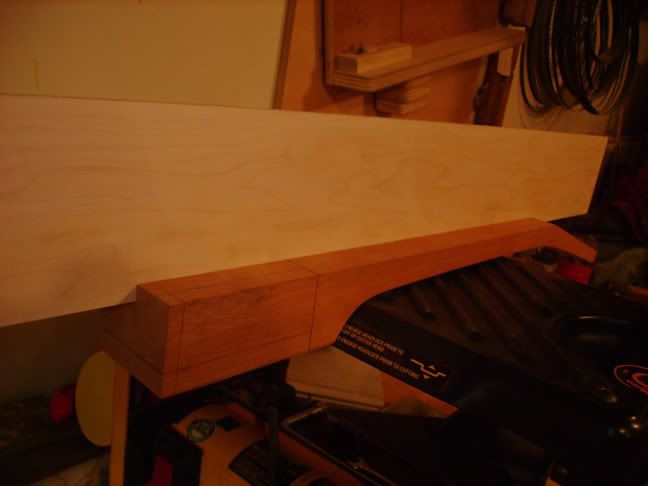
Next I marked out fret positions on the board and then used the curved truss rod jig to draw the curve on my filet.
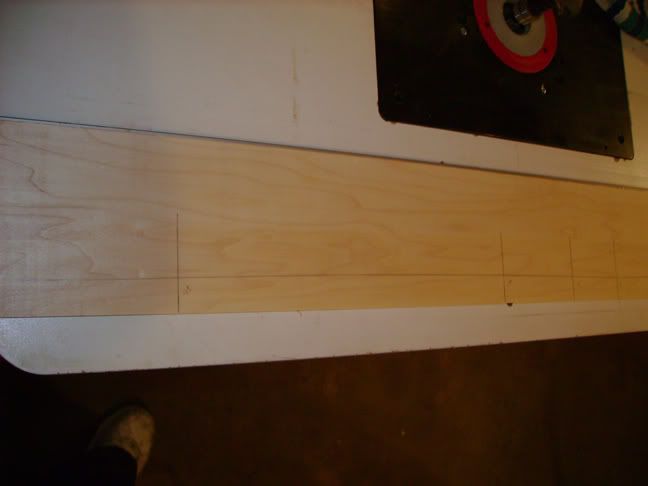
The truss rod access slot is the place where the truss rod sticks out at the headstock. This slot is necessary so that you can turn the truss rod nut with a wrench. To cut this slot I used a 1/2" bowl\cut bit (the top is shaped like a bowl). I put the fence on the router and set it so that the bit would follow the truss rod channel. I then adjusted the height of the bowl cut bit so that it would hit the headstock in the perfect place. I then ran the headstock over the bit about 1 1/2".
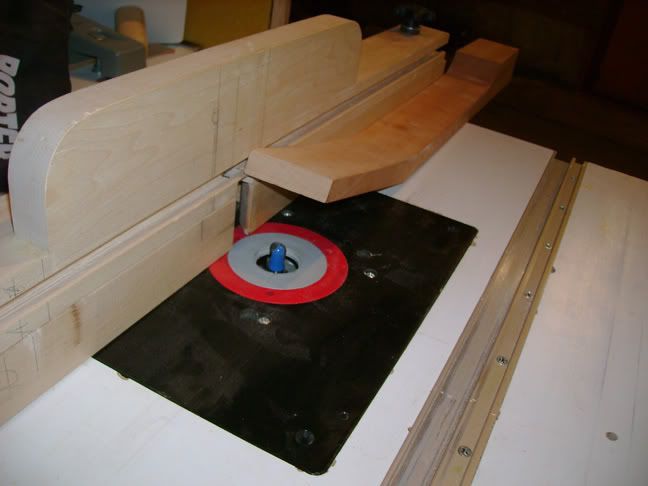
Here's what the channel looks like after being cut:
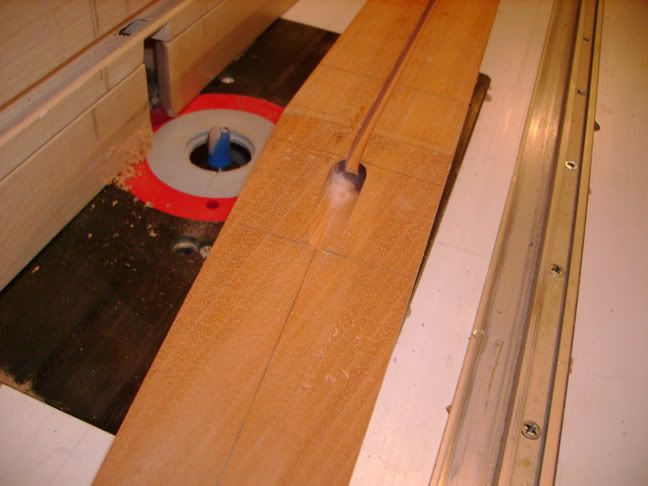
Honestly I wish I'd have used a 5/8" bowl cut bit just to make the slot a bit larger. I tried to widen the adjustment channel out with my Dremel but started to mess up the look of the slot so I quit. The washer and nut that fit on the rod must have a squared up area to rest against so I used a chisel to flatten the edge of the access slot. Here's what it looks like when the washer and nut are installed:
If you look at the washer you will notice that the top edge has been flattened. I flattened the edge with a bench grinder.
The other end of the truss rod must be anchored under the 21st fret. To accomplish this you must first trim the rod to the proper length and then use a tap on the end of the rod to cut the threads. When the threads are cut you can thread the anchor onto the rod. When the anchor is threaded as far as it can go you use a hammer to peen the excess rod up against the anchor so it will not turn. The proper tool for peening is a ball-peen hammer but I didn't have one. Instead my dad had this old hammer that worked about the same.
When the anchor is securely fitted to the rod you need to cut a slot for it in the neck. For this I used a forstner bit on the drill press. I can't remember what size I used but it fit the anchor perfectly.
I've seen some builds where the luthier mounted the anchor horizontal instead of vertical using a Dremel to hog out the necessary wood for the anchor slot. I'm not yet good with a Dremel (although I need to practice to do the inlays on the fretboard) so I chose to use the forstner bit and mount the anchor vertically. The anchor stuck up a tad so I used the bench grinder to whittle down one end a bit.
Back to the maple filet. I used the bandsaw to cut the curve on the filet and then smoothed it by hand sanding. I then fit the curved side down into the truss rod channel making sure that the fret markings on the neck and the filet matched up. When I pressed down on the filet I could feel the truss rod flex to accomodate the curve.
I decided I had a little too much of the filet sticking out of the topof the truss rod channel so I whittled it down using a disk sander. I almost forgot to make a smaller filet to fit the chanel on the other side of the anchor.
When I bought the wood for the filet I also bought some Tightbond Liquid Hide Glue. Hide glue is the traditional glue for luthiery. The reason hide glue is popular isn't so much that it holds well (although it does) but that parts glued together with it can be disassembled with a hot knife. The use of hide glue is the reason you can take the neck off a set neck guitar. The Tightbond version of hide glue is different than regular hide glue because it comes in a bottle. Regular hide glue is actually pellets that are dropped in a pot of water that is being heated by a hot plate. The pellets melt in the hot water and make glue. Kudos to Tightbond for inventing a more convenient version of hide glue.
Even my Tightbond Liquid Hide Glue wasn't without its quirks. I had it stored out in the garage where it is 45 degrees F. When I went to use the glue it had the consistancy of ballistics gel. I knew that I could warm up the hide glue by placing the bottle in a pot of warm water but I didn't want to wait. I pulled out the regular Tightbond II and used it instead. Tightbond II can also be a little thick when it's cold so I made sure the heat in the garage was at least 60 degrees F before gluing. Gluing the filet can be tricky because you do not want any glue leaking onto the truss rod. The easiest way to accomplish this is to only apply glue to the filet surface and not the walls of the truss rod channel. When you insert the filet into the channel the glue will the migrate up towards the top of the filet instead of down into the channel. After inserting the glued filet you then clamp it in being careful not to make sure the filet is tight but not TOO tight. Clamping also ensures that the rod bends to match the channel.
All these operations were being performed on NYE so I went party hopping for several hours before I came back and removed the clamps. Not to worry I also left the heat on in the garage while the glue was drying.
The next day I removed the clamps and inspected my work. Everything seemed fine so I preceeded to start trimming the filet flush with the neck. I used the disk sander to trim off most of the excess filet. When the filet was small enough I used my new 10mm IBEX finger plane to make the it very close to flush with the top of the neck. The finger plane proved to be the perfect tool and I only had to sand a bit to finish the job.
Whew, that went better than I'd hoped! I was feeling so good I decided to tackle fixing the neck mortice in the body. If you scroll back a few posts in this blog you will remember that I sort of screwed up the sides of the neck mortice. I fixed it by routing an additional 1/16" from each side of the mortice. Learning from past mistakes I was able to accomplish the fix without any errors. As you can see most of the burned wood on the sides is now gone. The small gash I made inside the mortice is also gone. Of course this alteration means I will have to widen the tenon on the neck an additional 1/16" on each side. No big deal.
My next task is to cut the tenon on the neck and the test fit the neck to the body. Hopefully I will have some time accomplish this during the weekend. I'm also starting to plan the top carve of the body.
I hope you enjoyed this submission. Please feel free to leave comments!
4 comments:
Wow, I see you are moving at a pretty high speed.
Glad to see everything is working out so well!
Reading this you've rekindled my desire to take up on working on guitars as well although I'm absolutely green when it comes to woodwork (not that I lack the skills but rather the tooling and instructions/time).
One day I hope...
KeeperOS from SDUGF
KeeperOS,
The great thing about this project is you don't need that many tools. I use things like a jointer and oscillating spindle sander because I have access to them.
To me the tools you really have to have are a decent router, a table saw, and a band saw. You don't need pro versions of these tools and get get them pretty cheap.
Great work . awesome ! thanks for sharing !
I have a question, I'm busy building a lap steel modelled conceptually off the National 'New Yorker' It's a series of laminated hardwood that make up the body and neck (one piece). It's looking great, the body has slightly bowed, about 1mm over 850mm. So my question is would it be possible to use a truss rod to straighten the body? I know conventually truss rods are used to adjust the neck, and that lapsteels don't normally have a truss rods. I'm thinking of using a truss rod on the bottom of the guitar to counter the box and the future string tension, could this work?
Thanks Zayne
Post a Comment